Most new industrial machines or retrofits require some form of connectivity to an existing communications infrastructure. From industrial fieldbuses to 3G cellular networks to web interfaces, even though each design has its own unique requirements, you can use LabVIEW to make the connection.
LabVIEW is a visual programming platform and development environment that can be used to support the connection of laptops and Programmable Automation Controllers (PACs), including CompactRIO, PXI/cPCI systems, and Industrial PCs (IPCs) to a variety of industrial networks and web technologies.

A CompactRIO programmable automation controller connected with the NI 9144 modular EtherCAT slave chassis over standard CAT5 cabling.
When coupled with PACs, this platform offers a superset of traditional PLC functions, making it easy to retrofit or upgrade an existing installation. PACs outperform PLCs in the areas of high-speed analog measurements and intensive processing algorithms needed for applications like machine condition monitoring (MCM) or machine vision. Because LabVIEW can interface to most industrial networks, PACs are commonly used to augment the PLCs in an existing machine or automation process to increase efficiency or predict maintenance of mechanical gearboxes and motors.
Integration to existing systems
The simplest way to integrate LabVIEW into an existing system is to use the basic analog and digital I/O capabilities of PACs and PLCs to exchange signals. LabVIEW will provide simple updates to a PLC system such as pass/fail status.
The simplest way to integrate LabVIEW into an existing system is to use the basic analog and digital I/O capabilities of PACs and PLCs to exchange signals. LabVIEW will provide simple updates to a PLC system such as pass/fail status.
For example, a customer used CompactRIO and LabVIEW to acquire a high-speed voltage reading from a gamma-based thickness sensor, and perform the complex inline signal processing required on that data to calculate an extremely accurate thickness measurement for the steel they were rolling. Then they output a simple analog voltage in the 0-10 V range that corresponded to the thickness of the steel over a cable connected to the existing PLCs controlling the rolling mill. The thickness measurement that the PLCs now use is more accurate than before and the customer can produce better quality and more consistent steel. In the end, they maintained their existing PLC control scheme but augmented it to build a better product.
That is just one example of how LabVIEW can be used with communication schemes. Here’s a quick overview of how to connect it to each of the popular industrial networks.
OPC
A widely used method to integrate multiple vendors’ automation controllers is OPC (OLE for process control). OPC is a Windows based standard for accessing industrial devices. Through the OPC client/server architecture, LabVIEW can integrate with a range of PLCs and PACs from a laptop or IPC. The OPC server manages the various industrial communications and provides a common bus for controllers, sensors, and actuators without physically wiring them together. You can use communication gateways as needed to extend to more specialized protocols.
A widely used method to integrate multiple vendors’ automation controllers is OPC (OLE for process control). OPC is a Windows based standard for accessing industrial devices. Through the OPC client/server architecture, LabVIEW can integrate with a range of PLCs and PACs from a laptop or IPC. The OPC server manages the various industrial communications and provides a common bus for controllers, sensors, and actuators without physically wiring them together. You can use communication gateways as needed to extend to more specialized protocols.
Modbus TCP and Modbus Serial
Modbus TCP and Modbus Serial are two of the more commonly used industrial protocols. Through multiple levels of functionality, LabVIEW supports Modbus TCP and Modbus Serial on any Ethernet or serial port on PCs or PACs. Through its graphical configuration assistant, you can create a Modbus TCP or Modbus Serial I/O server. LabVIEW can act as a Modbus master or slave and specify the different registers to read and write. In addition to the I/O server functions, there is a direct API to the Serial or TCP/IP versions of Modbus for flexibility and performance. That API can query or write to registers, coils, and discrete I/O. It can also check for exceptions.
Modbus TCP and Modbus Serial are two of the more commonly used industrial protocols. Through multiple levels of functionality, LabVIEW supports Modbus TCP and Modbus Serial on any Ethernet or serial port on PCs or PACs. Through its graphical configuration assistant, you can create a Modbus TCP or Modbus Serial I/O server. LabVIEW can act as a Modbus master or slave and specify the different registers to read and write. In addition to the I/O server functions, there is a direct API to the Serial or TCP/IP versions of Modbus for flexibility and performance. That API can query or write to registers, coils, and discrete I/O. It can also check for exceptions.
PROFIBUS
PROFIBUS is an industrial field bus originally developed in Europe. With more than 30 million installed nodes, it is the communication standard for Siemens Automation PLCs, smart sensors, actuators, and I/O. NI supports the more commonly used version of PROFIBUS, DP (Distributed Peripherals).
PROFIBUS is an industrial field bus originally developed in Europe. With more than 30 million installed nodes, it is the communication standard for Siemens Automation PLCs, smart sensors, actuators, and I/O. NI supports the more commonly used version of PROFIBUS, DP (Distributed Peripherals).
Our PROFIBUS PCI, PXI, and CompactRIO one-port interfaces function as masters or slaves, connecting to PC-based controllers. The interfaces include a stand-alone configurator and a LabVIEW driver for human machine interface (HMI) and SCADA applications. You can perform PROFIBUS device control or automated test using these interfaces.
EtherCAT
Published as part of the IEC 61158 specification, Ethernet for Control Automation Technology (EtherCAT) implements a master-and-slave architecture over standard Ethernet cabling, typically in a line topology. As a control bus, it focuses on deterministic, high-speed I/O for single-point applications such as machine control and motion.
Published as part of the IEC 61158 specification, Ethernet for Control Automation Technology (EtherCAT) implements a master-and-slave architecture over standard Ethernet cabling, typically in a line topology. As a control bus, it focuses on deterministic, high-speed I/O for single-point applications such as machine control and motion.
Both master and slave devices are available for use with EtherCAT. For the master controller, real-time PACs with dual Ethernet ports on the CompactRIO, PXI, and industrial controller platforms are available. There is also an EtherCAT slave with field-programmable gate array (FPGA) intelligence, the 8-slot NI 9144 chassis for C Series I/O modules.
EtherNet/IP
EtherNet/IP is also a real-time Ethernet protocol, managed by the Open DeviceNet Vendors Association (ODVA) and commonly found in Rockwell Automation (Allen-Bradley) PLCs. It communicates over standard Ethernet using TCP/IP and UDP/IP using a master (scanner) and slave (adapter) network architecture.
EtherNet/IP is also a real-time Ethernet protocol, managed by the Open DeviceNet Vendors Association (ODVA) and commonly found in Rockwell Automation (Allen-Bradley) PLCs. It communicates over standard Ethernet using TCP/IP and UDP/IP using a master (scanner) and slave (adapter) network architecture.
The EtherNet/IP Drive for Industrial Communication handles explicit messaging and adapter communication on this network. LabVIEW can use explicit messaging to read from and write to tags on a PLC supported by RSLogix 5000 and RSLogix 500. The adapter communication lets LabVIEW function as a slave (adapter), providing implicit I/O data to a remote PLC.

NIVarious USB, PCI, and PCMCIA FOUNDATION Fieldbus interfaces can control Fieldbus networks from LabVIEW.
DeviceNet
DeviceNet is another industrial protocol managed by ODVA and commonly found in Rockwell Automation (Allen-Bradley) PLCs. Unlike Ethernet/IP, which is based on the Ethernet physical layer, DeviceNet is based on the CAN physical layer and increases strength and interconnectivity by specifying various parameters, such as the required cable length, connectors, and baud rates.
DeviceNet is another industrial protocol managed by ODVA and commonly found in Rockwell Automation (Allen-Bradley) PLCs. Unlike Ethernet/IP, which is based on the Ethernet physical layer, DeviceNet is based on the CAN physical layer and increases strength and interconnectivity by specifying various parameters, such as the required cable length, connectors, and baud rates.
The DeviceNet for Control PCI and PXI master (scanner) interfaces manage and control a network of DeviceNet slaves. Included with these interfaces is the NI-Industrial Communications for DeviceNet software, which offers a high-level API that supports drag-and-drop I/O variables and explicit messaging function blocks. DeviceNet for Test interfaces for PCI, PXI, and PCMCIA have master (scanner) and slave (adapter) support, best used for testing DeviceNet products. The included test software consists of a configurator, analyzer, and the NI-DNET driver, which provides low-level functions.
CANopen
CANopen is a higher-level protocol based on the CAN physical layer and was developed as a standard embedded network with highly flexible configuration capabilities. Originally designed for motion control applications, it is common in many industry segments including medical equipment, off-road vehicles, public transportation, and building automation.
CANopen is a higher-level protocol based on the CAN physical layer and was developed as a standard embedded network with highly flexible configuration capabilities. Originally designed for motion control applications, it is common in many industry segments including medical equipment, off-road vehicles, public transportation, and building automation.
For CANopen master function, the CANopen LabVIEW Library has high-level, easy-to-use functions to create CANopen master applications. These functions cover the spectrum of CANopen master applications, including transmitting and receiving service data objects (SDOs) and process data objects (PDOs), network management, heartbeat and node guarding, emergencies, and synchronization objects. Because the CANopen functions work on top of NI-CAN driver software, all PCI, PXI, and PCMCIA high-speed NI Series 2 CAN devices can operate as fully functional CANopen master interfaces.
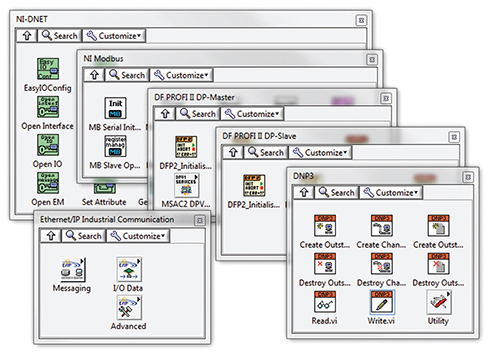
DeviceNet, Modbus, Profibus, DNP3, and EtherNet/IP are some of the industrial networks supported in LabVIEW.
DNP3
DNP3 (Distributed Network Protocol) was developed by GE Harris to create a standard protocol specification for vendors of power grid SCADA (Supervisory Control and Data Acquisition) components. Since 1993, this open and public protocol has been managed by the DNP3 Users Group. DNP3 is commonly used in North American electric and water utilities for communication between SCADA masters and outstations like Remote Terminal Units (RTUs).
DNP3 (Distributed Network Protocol) was developed by GE Harris to create a standard protocol specification for vendors of power grid SCADA (Supervisory Control and Data Acquisition) components. Since 1993, this open and public protocol has been managed by the DNP3 Users Group. DNP3 is commonly used in North American electric and water utilities for communication between SCADA masters and outstations like Remote Terminal Units (RTUs).
The Industrial Communications for DNP3 software driver programs LabVIEW targets DNP3 outstation devices with such functions as power quality monitoring, phasor measurements, and other smart grid-related analysis. Because DNP3 is built on standard Ethernet, the NI implementation of DNP3 is portable across multiple LabVIEW supported platforms, including Industrial PCs, PXI, and CompactRIO. The DNP3 software driver supports Ethernet communication, file transfer, and time synchronization between master and outstation. Also, multiple communication channels per outstation and multiple sessions (logical devices) per channel may be used.

PCI, PXI and CompactRIO PROFIBUS DP interfaces can be set for master and slave support.
FOUNDATION Fieldbus
FOUNDATION Fieldbus is a bi-directional serial communication protocol commonly used in process automation. It uses a system of distributed control with intelligent devices, where the control schedule can be downloaded onto the devices instead of a central control system. Of its two versions, NI interfaces support H1.
FOUNDATION Fieldbus is a bi-directional serial communication protocol commonly used in process automation. It uses a system of distributed control with intelligent devices, where the control schedule can be downloaded onto the devices instead of a central control system. Of its two versions, NI interfaces support H1.
The USB-8486, PCI-FBUS, and PCMCIA-FBUS series interfaces connect these fieldbus’s devices to standard desktop, industrial, and notebook PCs. With the PCI-FBUS, an IPC can act as the host within this protocol system. Use the USB-8486 and PCMCIA-FBUS for portable data logging and in-the-field configuration and maintenance of devices and networks.
Web and Enterprise connectivity
Enterprise connectivity is also playing a larger role in deployed systems so that off-site users can view the real-time data and change system parameters on the fly. LabVIEW graphical tools provide functions for Web-published software interfaces, Web services, common gateway interface programming, short message service (SMS), and e-mail messaging. In combination with HTTP and FTP servers on CompactRIO, these functions can be used for remote monitoring and control, phone or e-mail alerts, and file transfers of logged data. Leveraging NI third-party partners, you can share data via global cellular networks or synchronize global processes via GPS in LabVIEW.
Enterprise connectivity is also playing a larger role in deployed systems so that off-site users can view the real-time data and change system parameters on the fly. LabVIEW graphical tools provide functions for Web-published software interfaces, Web services, common gateway interface programming, short message service (SMS), and e-mail messaging. In combination with HTTP and FTP servers on CompactRIO, these functions can be used for remote monitoring and control, phone or e-mail alerts, and file transfers of logged data. Leveraging NI third-party partners, you can share data via global cellular networks or synchronize global processes via GPS in LabVIEW.
No comments:
Post a Comment